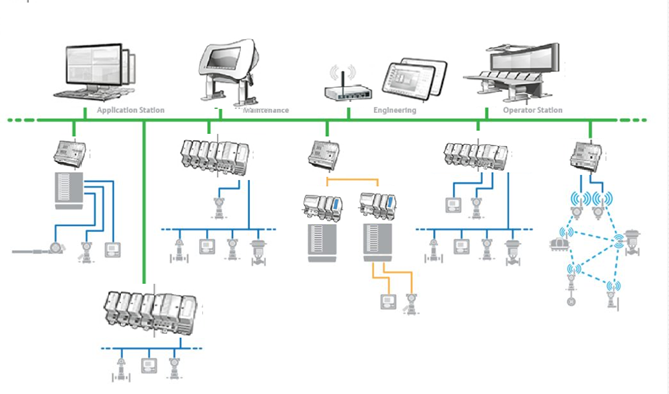
DCS and PLC Systems
With the rapid advancement of technology from the past to the present, the production and operation process of products has also begun to change in parallel. As the processes and products to be developed are processed in a “smart” and customer-focused manner according to the needs of the customers, the solutions are expected to be faster and more reliable in order to meet these needs within a competitive environment. This complex system that emerged has prompted the question of integrating fundamental elements involved in the process with the internet, mobile devices, sensors, and other smart devices. As a result, the development of small, medium, and large-scale control systems has accelerated.
In today’s world, industrial applications and automations operate through control systems. An Industrial Control System (ICS) defines a general control system that plays a fundamental role in system setups that utilize distributed control systems (DCS), SCADA (Supervisory Control and Data Acquisition) systems, and programmable logic controllers (PLC). The primary goal in these small-scale control systems is to process industrial automation processes more efficiently, easily, and quickly.
There are two types of controls that can be used in the production process. One is the Programmable Logic Controller (PLC) and the other is the Distributed Control System (DCS). Since Programmable Logic Controllers (PLC) and Distributed Control Systems (DCS) play a tool role in controlling complex production processes, the two terms are often used interchangeably. Although these two control systems have a similar operating logic, their applications are quite different.
PLC (PROGRAMMABLE LOGIC CONTROLLER)
The PLC used for industrial automation is a hardened computer responsible for the electromechanical control of equipment that makes up the production lines in facilities.
PLC is a microprocessor-based device that has replaced control elements such as relay cards, auxiliary relays, timing relays, and counters used in automation circuits. A PLC consists of four main parts that ensure its reliable and efficient operation:
- CPU (Central Processing Unit)
- Memory Unit (RAM – ROM – PROM)
- Input Unit (INPUT)
- Output Unit (OUTPUT)
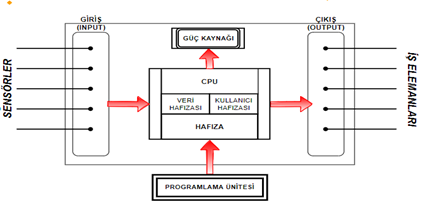
PLC receives information from connected sensors or input devices, processes the data, and triggers the output points according to pre-programmed parameters. Depending on the input and output points, a PLC serves to monitor and record digital and analog data such as machine productivity, operating temperature, and operating duration, to automatically start and stop processes, and to create alarms if a machine fails.
Programmable Logic Controllers (PLC) are flexible and robust control solutions that can be adapted to almost any application area. In the field of industrial automation, control, data acquisition, data processing, communication, arithmetic, counting, comparison, data transfer, and other analytical processes enable the management of the entire system through analog and digital input-output points.
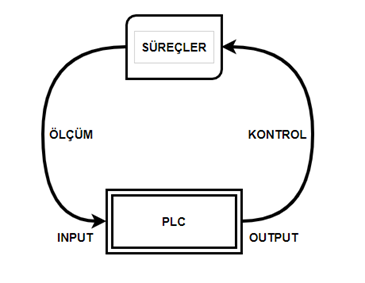
The basic working logic of the PLC depends on the programming technique. The working logic of a PLC with its programming technique:
- The logic values (1 or 0) read instantly from the input points are stored in memory.
- The input data is read and interpreted according to the program written inside the PLC.
- A decision mechanism is created to carry out communication processes at certain points.
- The data transferred to the output points is set to be logical 1 or 0 (usually expressed as 24V or 0V).
- The PLC performs this input and output operation at a millisecond speed.
DCS (DISTRUBTED CONTROL SYSTEM)
Within a facility, each object is used for many purposes such as data collection, data storage, graphical analysis of data, data display, process control, data transfer, and feedback. These objects, which appear independent, are controlled through a computer connected to the facility’s local network. This network of distributed sensors and controllers controlled via a local area network is known as DCS. The real-time, automatically decision-making DCS system is also known as the central brain of the facility.
To briefly explain, DCS are comprehensive systems that allow distribution from a single point by collecting multiple pieces of information from different locations.
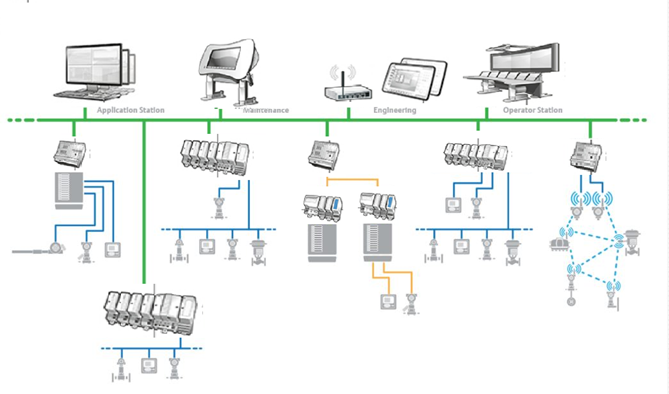
In areas where Process Automation is continuously present, viewing control and command rooms without a DCS system is quite difficult. DCS stands out with many advantages such as ease of maintenance and repair in the facility, easier monitoring of many parameters at the same time, more reliable control, and overall optimization.
The main point of DCS is having a central network system. All units mentioned are connected to this central network point and provide reliable and fast real-time communication with each other.
SIMILARITIES AND DIFFERENCES BETWEEN DCS AND PLC
DCS, being a more comprehensive system than PLC, has been formed by the combination of many PLCs and computer systems. Looking at this situation, it can be said that DCS is a larger-scale system that encompasses PLCs as needed.
In terms of similarities, functional blocks are present in both DCS and PLC systems.
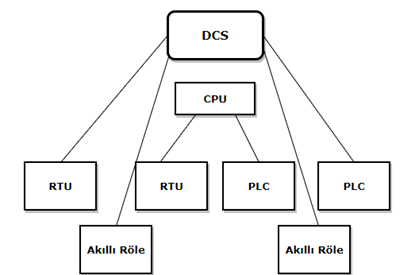
DIFFERENCES BETWEEN DCS AND PLC
- Reaction Time
PLC is preferred in systems with high digital IO density, DCS is preferred in systems with high analog IO and PID control density. However, this should not mean that PLCs cannot process analog data. - Programs They Use
- DCS
PLC
PLC One for everything
Programming program is sufficient.
Field Bus (DP, FF) Engineering Workplace
Application software with Communication (Ethernet, Serial),
Hardware hardware, field bus,
Field Devices communication is covered.
Separate program is required for Process Graphics.
- DCS
- Scalability
PLCs have less IO capacity than DCS. For this reason, DCS adapts more easily to new equipment and is easily used in large-scale projects. PLC is not as scalable as DCS and is preferred in small plants.
PLCs are still used in RTU stations due to their small and inexpensive architecture and engineering (typically RTU application) instead of large DCS.
At the same time, PLC is suitable for specialized applications that change less frequently, while DCS is suitable for complex processes that require advanced process control capability. - Update/Upgrade/Modernization
Update process in PLC,
Version differences,
Most of the remaining programs in the PLC will be updated separately,
It is very difficult due to possible problems with vendors.
The update process in DCS can update the DCS controller to the next version in just a few minutes.
In this case, updating is much easier in DCS than in PLC. - System Density
If a simple system needs to run quickly, a PLC should be used; if the system involves many complex operations in succession, a DCS should be used. In addition, if there are many input and output points in the system where the process takes place, a DCS system is preferred because it would be difficult to bring many equipment together in a PLC. - Process Change Frequency
PLCs are automation systems that can produce efficient results in stationary systems. DCSs, on the other hand, are more preferred when it comes to analyzing a large amount of data, often requiring a series of different operations. - Redundancy
DCS system is more preferable than PLC system in terms of redundancy. This is because PLCs can be made redundant with additional hardware which makes them more expensive than DCS. - Architecture and Cost
PLCs have a simple and flexible architecture. A PLC system consists of controllers, IO modules, HMIs and an engineering software.
DCS systems are less flexible and complex. They consist of controllers, IO systems, database servers, engineering and operating servers.
Because of these components, PLC is a less costly system than DCS. - Communication
PLC
It is a single product.
PLC does not know other PLCs in the system.
An engineering infrastructure is required to communicate with other PLCs.
Powerful CPUs have been developed because they cannot be shared between applications. Therefore, the cost may increase.
DCS
It works as a system
Any variable becomes globally shareable by all DCS controllers.
No additional engineering is required for communication. - Faceplate Concept and Alarms
PLC
The desired faceplate should be selected according to the requirement.
It is necessary to establish a connection between the PLC program and the process graphics and to adapt the alarms to the process graphics.
DCS
When PID Controller or pump block is created in DCS program, it will work together with faceplate alarms. In this case it will be more advantageous to use DCS.